Discovering the complex world of maintenance shutdowns at nickel plants requires immersion in the experience of a seasoned professional. To this end, we interviewed Yves about his role as Lead Executor for various maintenance shutdowns at nickel plants in New Caledonia. We take a look at his fascinating career path.
What is your career path?
Yves: My career path began in 2011, when I took part in the construction of a nickel plant for a major player in the mining and metallurgy sector in northern New Caledonia. After the plant was built, I was involved in commissioning and rebuilding the pyrometallurgical furnace. My familiarity with this equipment enabled me to supervise the rebuild. In 2021, I was called back to coordinate and supervise technical shutdowns, accepting the role of Lead, with usual durations of 7 to 9 weeks.
What does the role of Lead for a maintenance shutdown entail?
Yves: My role as Lead involves taking responsibility for the entire technical shutdown. As Lead, I play the role of coordinator, sometimes called manager. With some 200 to 300 subcontractors working in the plant, my job is to coordinate their activities. Under my supervision, a team of zone technical managers and supervisors oversee and coordinate the various jobs carried out by the subcontractors. This includes trades such as boilermakers, mechanics, welders, electricians, instrument technicians...
How do you coordinate the teams?
Yves: To coordinate subcontractors effectively, we need to provide them with a variety of equipment, such as scaffolding, clean work areas, vacuum trucks, cranes and other shared resources.
We hold coordination meetings morning, evening and night to align everyone's needs and allocate resources efficiently. This can sometimes involve priorities, where some subcontractors get equipment first while others have to wait.
Our main role is to ensure that all subcontractors work safely, that the work meets the plant's quality standards, and that the schedule is adhered to. We juggle these three major objectives in a period generally limited to 4-5 weeks. Although deviations may occasionally occur, we must constantly justify why and ensure that the work is carried out safely, to the required quality and on schedule.
Are you involved in maintenance shutdown planning?
Yves: As far as planning is concerned, I'm not directly involved in setting up the schedule. I come in two or three weeks before the start of the shutdown. At this stage, the schedule is generally 95% established, but my involvement consists in understanding the underlying strategy. If necessary, I work with the team to readjust the schedule preconceived by the Major Shutdown Unit. When I arrive, my main role is to take charge of the worksites, as their precise nature is not known three weeks beforehand. Although 80% of the work consists of standard recurring jobs, it's crucial to reorganize these operations and distribute them among the supervisors. Supervisors arrive on site around ten days before plant start-up, and I make sure they have a clear brief, detailing their scope of work based on documents prepared by the preparers.
What is your role in terms of safety?
Yves: As far as safety and training are concerned, I don't have a training role, but I make sure that everyone involved is properly trained. Every consultant is obliged to train his or her staff in working at heights and confined spaces. In addition, I play a communication role by organizing daily presentation meetings during the 15 days prior to start-up, covering safety topics specific to the plant. I also hold start-up meetings every morning during the worksite to relay safety messages from the previous day.
What are the qualities of a good Lead?
Yves: As far as the role of Lead on a maintenance shutdown is concerned, it requires considerable energy and a constant presence. The term "orchestra conductor" is appropriate, as it involves coordinating and managing all operations to achieve the objectives set. There's constant pressure, but it's also an exciting challenge. Each maintenance outage is unique, bringing new challenges and requiring us to constantly question our working methods.
In short, the role of lead on a maintenance outage requires passion, commitment and the ability to handle pressure. It's like a marathon where, despite the fatigue, the satisfaction of bringing the project to a successful conclusion is always present. I appreciate this dynamic and the chance to learn continuously in this demanding field.
Finally, how would you describe your experience as a consultant?
Yves: When it comes to working with Easy Skill, I appreciate the team's rigor and professionalism. Easy Skill stands out for its attentive follow-up and constant presence. The teams are friendly, and it's a team I enjoy working with, and with whom I've been collaborating since 2021.
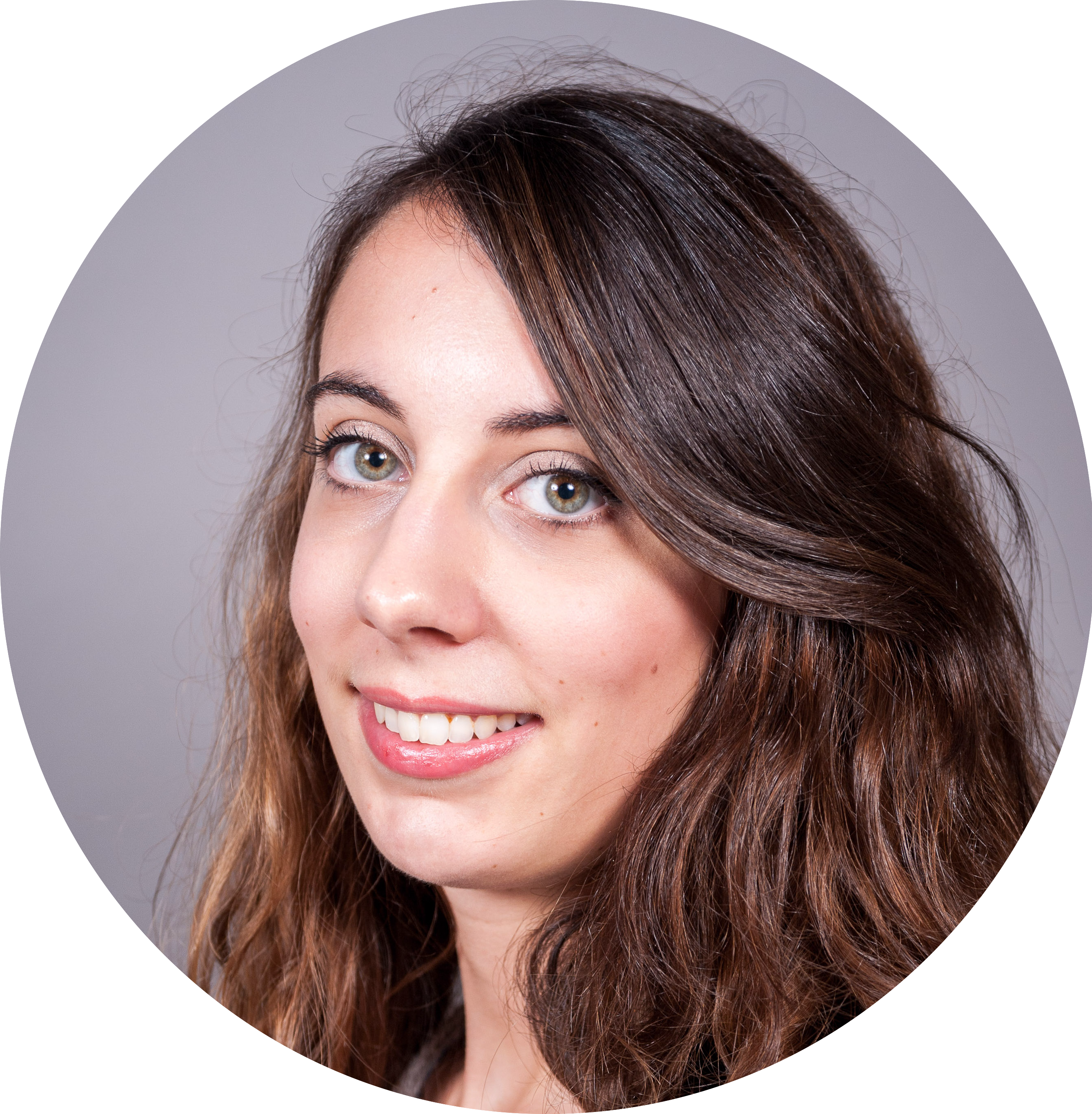
Lauriane Pellaud
Marketing Coordinator and creative pro. She enjoys simplifying complex topics into simple narratives to engage audiences and communities. Food lover and seamstress in her spare time.
Share this Article