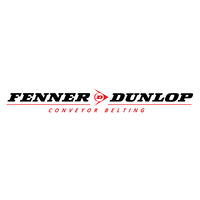
Upskilling Workforce to Supply the Mining Industry
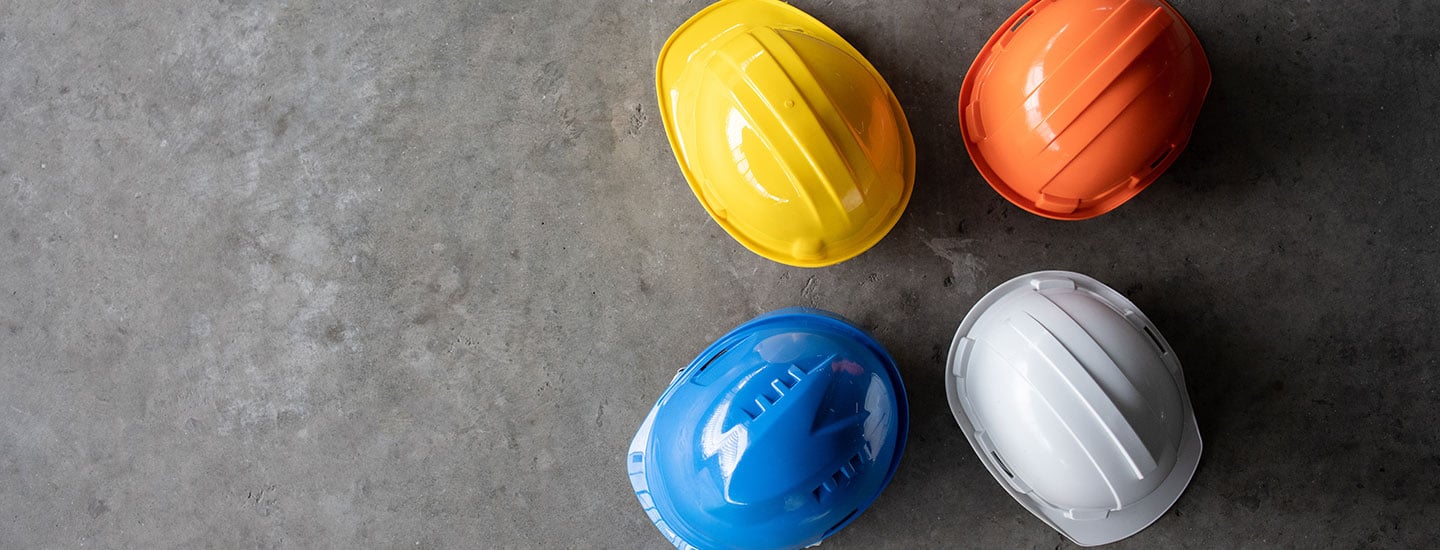
Meet the project
Fenner Dunlop is the world’s largest manufacturer of engineered conveyor solutions for mining and industrial industries. Inspired to provide flawless safety and unparalleled reliability, they are known for building products that last. With almost 1000 Australian employees, safety and continuous improvement programs are a cornerstone of the business.
Fixed plant systems like conveyor belts add
major potential hazards. Between heavy machine components, constant motion, drives, gears, and cables, working on the conveyors can be a dangerous job. In order to ensure a safe work environment, Fenner provides an annual rigorous training program for their internal assessor team to ensure the entire company upholds the national safety benchmark.
Building their internal assessor team relies on an annual 10-day training program to keep knowledge current. Pandemic travel restrictions made single venue delivery impossible. They shared concerns over self-paced online learning and decentralisation with multiple providers. So Easy Skill was hired to provide an innovative training solution to create a blended learning model with live virtual instruction for the national accreditation program.
Easy Skill created a virtual training session with a live instructional designer. Animated video was chosen to simulate the classroom environment and ensure optimal learner engagement. As a result, 20 national internal assessors achieved 100% completion. Fenner enjoyed the quick and stress-free delivery of a flexible training model that met their national business needs, while also saving thousands in travel costs.
The context
What the client says
Changing the world
Workplace accidents are steadily declining,
but Fenner has a commitment far beyond
compliance. They are excited to create
rigorous monitoring and training programs to
ensure daily safe operations for all plants and
equipment. By proactively training all internal
personnel on proper safe work procedures, they
effectively minimise the risk of working with
large, complex machinery.
Conveyor belts are extremely versatile which
makes them very popular in manufacturing,
construction, production, warehousing, and
distribution centres. While in operation, belts
rely on a mix of safety measures like isolation,
engineering controls, PPE, and continuous safety
monitoring. However, when under construction
or maintenance many of those safety measures
cannot be maintained as employees need
access to the machinery.
The fleet of 20 national internal assessors
provides local safety training and evaluation
to ensure all employees are adhering to safety
best practices throughout their daily activities.
Delivering one centralised training program
annually ensures they have the latest safety
knowledge, while also standardising safety
mandates across the country.
Industrial clients rely on Fenner to deliver the
toughest conveyor solutions that are built to
last without compromising the safety of their
teams. The internal assessor training program
is the essential foundation for the company
to ensure they continue to meet and exceed
customer expectations.
Evaluating the health, performance, safety, and
productivity of each and every conveyor system
is the extra peace of mind Fenner Dunlop is
known for. They achieve this by ensuring there
are always a minimum of 20 internal assessors
proactively carrying out their vision for optimal
health and safety, while continuously evolving
their knowledge, activities, and effectiveness.
The big wins
- Travel-free National Training
- Creative Blended Training Model
- Saved Stress + Money