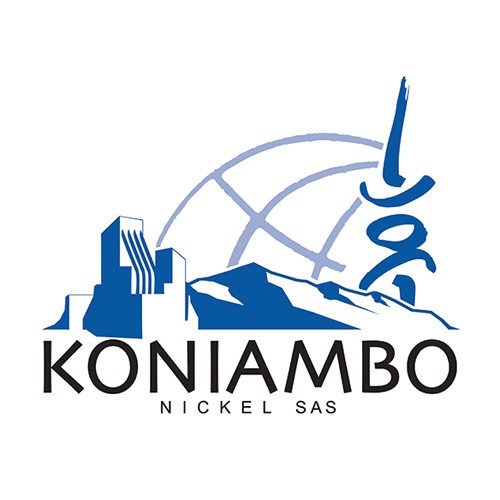
Mobilising an Automation Expert in a Remote Mining Area
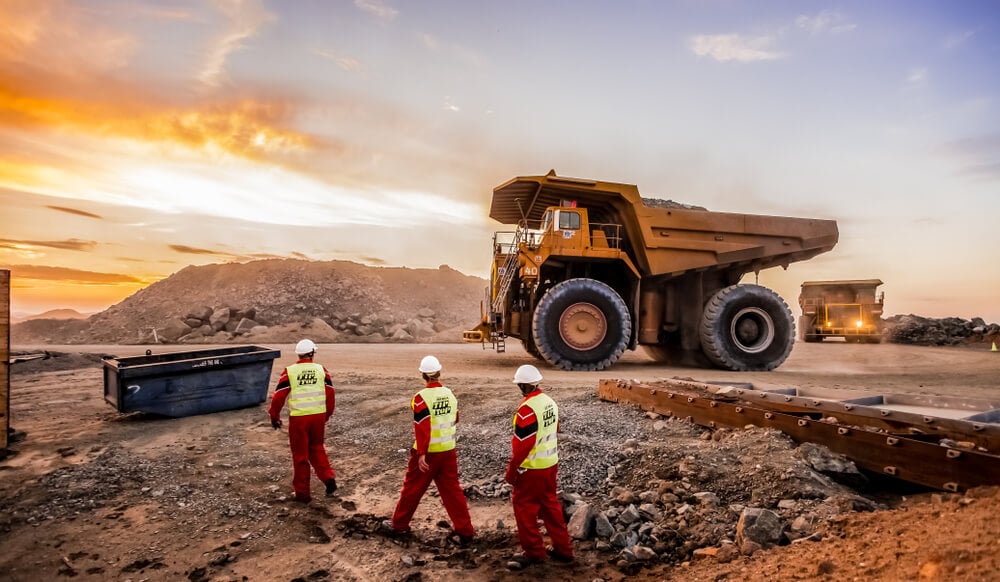
Meet the project
Koniambo Nickel SAS (KNS) has a production capacity of 60 000 tons of Nickel per year. To reach this production target, it heavily relies on very specific engineering expertise. Notably, the industrial complex needs a large amount of water to ensure the regular operation of the plant. It requires a desalination unit, treating 20m3/h of seawater pumped from nearby.
There were recurring issues with the automatic
sequences that drive the desalination unit. System incompatibilities between the KNS standard code and the code of the desalination unit were causing severe breakdowns. Modifying the interface of the desalination unit had to be done live without stopping production. Yet, this specific skill is not available on the island.
Easy Skill found a skilled automation engineer able to answer the tough challenge. He was a former KNS employee who had returned to France. As the consultant’s constraints were not compatible with a regular local employment contract, Easy skill quickly offered an innovative and agile solution. The consultant works six months remotely from France and six months on-site for the implementation.
Doing the operation from design to commissioning by an expert is a real challenge in agility and coordination with the production team. The automation engineer was able to diagnose the process, improve the interface to allow first level operators to use it and enable an efficient maintenance strategy, reducing downtime and lower production. As it fits the expert and the company’s needs, the collaboration has been successfully ongoing for the last two years and a half and is planned to continue.
The context
What the client says
Changing the world
Koniambo Nickel SAS operates a world-class industrial site that functions according to the principles of sustainable development and guarantees a competitive cost price. This positioning makes it one of the most competitive ferronickel production sites in the world. However, the global skills shortage in the mining industry is becoming a real issue for KNS, like for every mining player.
Providing flexible workforce options is an innovative way to attract more engineering skills to work in a remote mining area. If rosters are usual practice for the mining sector, they can be more challenging to put in place between faraway territories. In the context of travel restrictions and to avoid unnecessary travel costs due to rosters, suggesting a half year of remote work and a half year on-site can make sense in many cases.
The integration of a skilled automation engineer and former employee of KNS had many positive impacts.
First, the consultant provided a new sequencing system in coordination with the operational team to prevent stopping the mining production.
Second, the recurring breakdowns interrupting the production were dramatically reduced.
Third, the time saved on diagnosis and troubleshooting enabled the training of first level operators to understand the problems and provide reports. It’s taking an intense workload off the engineering team.
The big wins
- Attracting an expert to a remote area
- Flexible workforce solution
- Productivity and efficiency maintained